Function description
Damage caused by production line stoppages and damage to equipment and machinery due to the presence of iron parts such as loader nails and rebar separated from machinery has always been a problem in industrial factories and mines. PMEA series electro-magnetic separators minimize these damages by absorbing these parts and discharging them outside the line. The self-cleaning system is also very suitable for continuous separation of iron parts and particles in lines with high and widespread iron contamination (such as sand and waste recycling lines).
Application
Protecting equipment such as crushers, mills and conveyor belts from iron parts – separating iron parts from raw materials and purifying raw materials – suitable for cement factories – gypsum – brick – lime – sand and gravel – recycling of foundry sand – silica – glass and ceramic raw materials – all mines and mineral concentrates – copper and aluminum industries – lead input – sugar and sugar – animal feed – paper – wood – slag – and petrochemical industries
Benefits
Very high absorption power – Ability to install at a great distance from the conveyor floor 600 (mm) – Easy operation and maintenance – No need for a cooling system (Natural Air Cooling) – Continuous operation capability (CDF 100%)
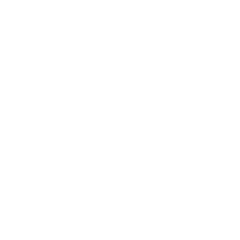
Production diversity
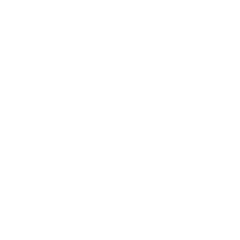
24month product warranty
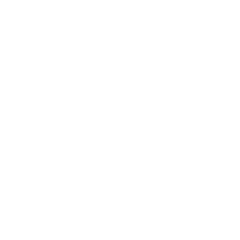
10year parts support
- Precise control of vibration amplitude by the operator
- Standard design with production line position
- Design in different capacities
- Instantly reduce and increase the amount of food
How to install
The PMEA model magnetic separator can be easily installed on the top of the conveyor belt or chute using a wire rope and four magnet earrings. If the longitudinal installation method is used, that is, installation at the drop location, the end roller of the conveyor belt must be made of stainless steel.
The main factors in selecting the PMEA model of the fixed electric magnetic separator
are the maximum distance of the magnet installation from the bottom of the conveyor belt or chute.
The PMEA model magnetic separators are usually installed at a distance of 7-10 (cm) from the surface of the passing load. Therefore, to select the appropriate magnet, the maximum crown load of the passing material must be considered and the magnet installation distance must be considered by adding 7-10 (cm) to it.
Material passing speed
In effective separations, iron pieces must be under the influence of the magnetic field for at least 0.4 (s). If the speed of the passing materials is high, magnets with a wider width should be used. For example, if the speed of the conveyor belt (or materials) is 1.5 (m/s), the minimum width of the magnet should be 60 (cm).
Volumetric mass of the passing materials (density)
The higher the mass of the material, the more difficult it is to separate iron pieces from the material. Therefore, in cases where the density of the material is less than 1 (gm/cm), smaller magnets can be used.
Size of iron parts
The larger the volume or weight of the iron pieces to be absorbed, the easier they are to separate.